The 5 most common faults when implementing Lockout-Tagout-Tryout and how to prevent them
- Posted on
- 0
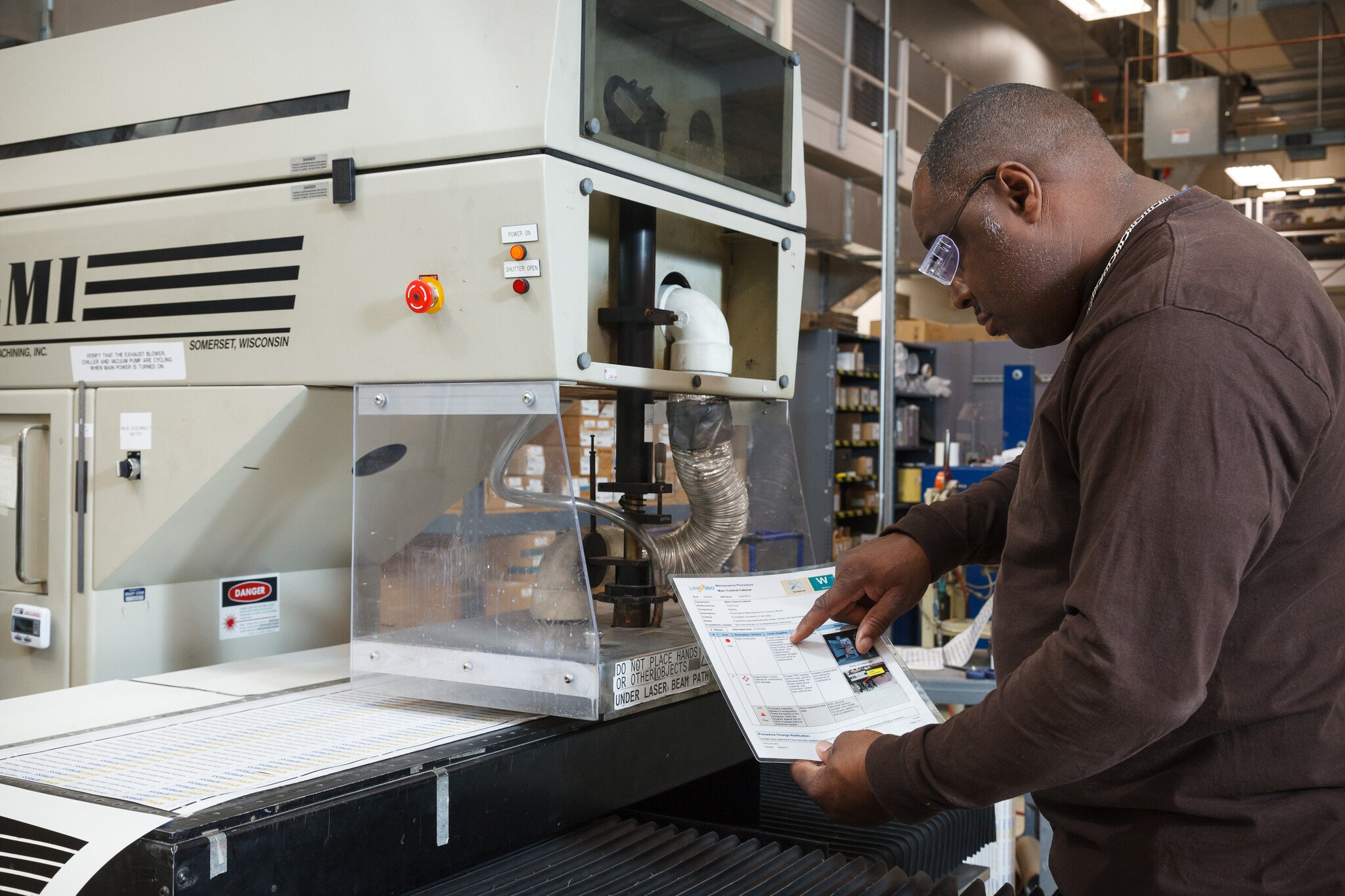
Lockout-Tagout-Tryout (LOTOTO) is a critical safety procedure for preventing machinery from being accidentally energized, protecting workers during maintenance and servicing. However, implementing Lockout-Tagout (LOTO) can come with challenges. Here, we discuss the five most common faults made during LOTO implementation and how to effectively address them to ensure a safer workplace.
1. Incomplete Identification of Energy Sources
One of the most common issues in LOTO implementation is the failure to identify all hazardous energy sources associated with equipment. Energy sources can include electrical, hydraulic, pneumatic, mechanical, thermal, or chemical sources. Missing even a single energy source can lead to a dangerous situation.
How to prevent this: Conduct thorough energy source assessments for each piece of equipment, ideally using standardized forms or checklists. Engage workers who are familiar with the machinery to help spot overlooked energy sources and ensure that every possible hazard is documented.
2. Lack of Employee Training
LOTO procedures are only effective if all workers are properly trained. A common mistake is insufficient or inconsistent training of employees involved in LOTO operations, including those who are new to the team or have recently changed roles.
How to prevent this: Ensure a comprehensive training program is available, covering LOTO procedures, risks, and the specific roles of authorized and affected employees. Training should be ongoing and include refreshers, practical drills, and updated training for new equipment.
3. Failure to Verify Isolation
Simply locking out equipment does not always guarantee it is fully de-energized. Many LOTO incidents occur when workers fail to verify that energy has been isolated before starting work.
How to prevent this: Verification of isolation should be a mandatory step in LOTO procedures. After applying lockout devices, workers must test the machine to confirm there is no residual energy. This verification process should be clearly documented as part of every LOTO checklist.
4. Incorrect Use of Lockout Devices
Using incorrect or incompatible lockout devices, such as clamps that don’t fully secure a valve or locks that are easily bypassed, can undermine the entire LOTO process. Improvising with the wrong tools can lead to severe accidents.
How to prevent this: Invest in purpose-made LOTO devices and ensure workers have access to the right tools. Conduct periodic audits to ensure proper use and condition of lockout devices, replacing worn or unsuitable equipment.
5. Insufficient Communication
LOTO procedures require clear communication between everyone involved, from machine operators to maintenance workers and supervisors. Poor communication can result in safety padlocks being removed prematurely or failure to notify all affected personnel.
How to prevent this: Establish clear communication channels and documentation protocols for LOTO procedures. Use lockout tags with complete information and ensure that shift changes or handovers include discussions about ongoing LOTO processes.
Complementing LOTO with Alpha and Bravo Entrapment safety guards
In addition to LOTO, mechanical safeguarding solutions like the Alpha and Bravo entrapment guards can be an effective way to enhance worker safety. These devices help prevent access to hazardous areas by physically locking access points, preventing unintended entry when dangerous conditions may exist. By integrating Alpha and Bravo with LOTO procedures, organizations can add an additional layer of safety, ensuring that hazardous areas are securely closed off until the lockout process is fully completed and verified.
Implementing Lockout-Tagout-Tryout effectively is crucial to maintaining worker safety. Avoiding common faults like incomplete energy identification, insufficient training, poor device usage, inadequate verification, and miscommunication can significantly enhance LOTO practices. By also incorporating mechanical safeguards such as Alpha and Bravo entrapment guards, companies can ensure that maintenance activities are performed in the safest possible environment.
Comments
Be the first to comment...