Work on your 5S workplace in the new year!
- Posted on
- By Birgit
- 0
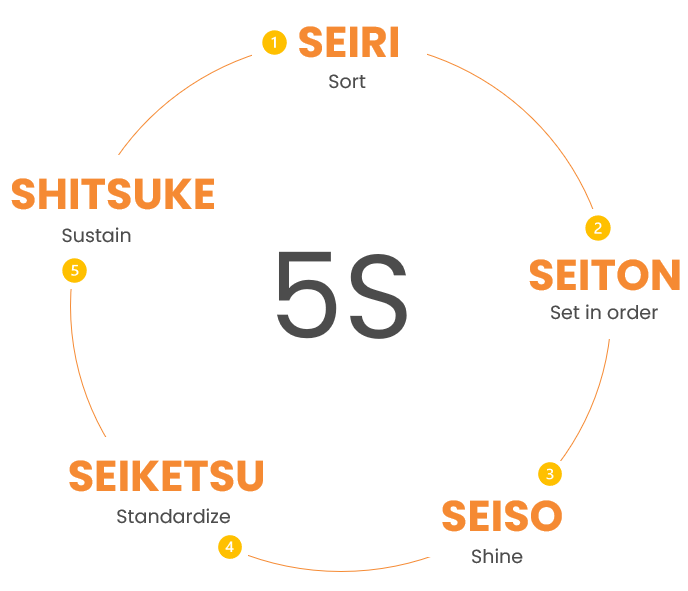
The 5S method is a systematic approach within Lean management that helps create an organised, safe and efficient workplace. Originally developed in Japan, the method is used worldwide to optimise the workplace and promote a culture of discipline and continuous improvement. The name ‘5S’ refers to five steps beginning with the letter ‘S’ in Japanese, English and Dutch. Here is a brief overview of the five steps:
- Sort (Seiri) - Identify and remove all unnecessary items from the workplace to keep only what is actually needed. This creates an uncluttered, safe and efficient environment where less space is wasted and employees can concentrate on their work without distractions.
- Set in Order (Seiton) - Make sure each item has a logical, fixed place that is eassily accesible. By organising everything and making i visually recognisable, search time is minimised and employees can work faster and more efficiently. This promotes a streamlined workflow and avoids unnecessary delays.
To arrange the workplace correctly, you can use our key cabinets, here you can store all your keys conveniently. At Lockout-Tagout-shop.com, you will find all kinds of key cabinets for different numbers and shapes of keys.
You can use lockout stations and padlock stations to conveniently store your lockout tagout materials. Lockout stations are easily identifiable and attachable storage locations that provide orderly and clearly visible storage.
If you want to store keys safely, you can use the key safe for maximum safety.
To organise your keys, folders, storage spaces, etc., you can use labelling. Using our label printers, this is very easy.
S-hooks (cabel hooks) to ensure that wiring stays neatly in a fixed and safe place outside walkways and work areas. Hang your cables and wiring safely and conveniently with CableSafe's safety hooks. This prevents accidents and gives you an orderly workplace.
For an even more optimal workplace, you can use a personalised Lockout-Tagout magnetic shadow board, available in various sizes. These shadow boards optimise lockout-tagout procedures by clearly linking materials, work permits and procedure.
- Shine (Seiso)– Ensure that the workplace is cleaned regularly to maintain a safe and productive working environment. A clean workplace not only reduces accident risks but also makes it easier to spot and address abnormalities, such as wear and tear or defects, quickly. This helps prevent problems and keeps equipment in optimal condition.
- Standardize (Seiketsu) – Create clear standards, such as visual aids, checklists and procedures, to ensure the order and tidiness achieved with 5S. These standards ensure that processes are carried out consistently, regardless of who performs them, and that improvements are permanently embedded in daily operations.
- Sustain (Shitsuke) – Encourage discipline by training and giving employees responsibility in following 5S principles. Provide regular reviews and feedback to reinforce and structurally improve the application of 5S. By paying continuous attention to sustaining, a culture of continuous improvement is achieved.
Together, these steps help to continuously optimise the workplace and foster a culture of efficiency and engagement.
Comments
Be the first to comment...